Product Description
Product Description
1200Meter rotary table truck mounted water well drilling rig
1.HRMC-1200 is a truck mounted and a rotary table drilling rig.
2.The truck chassis adopts the special heavy truck chassis, the main transmit, transmission power, gearbox, sets of winch, mud pump, diesel engine and mast are set up on the chassis.
3. The rig is a rotary drilling rig with directional circulation, which is equipped with mud pump. It adopts the slurry as the washing fluid, it can drill on clay, sand and rock if it is connected with the suitable drilling bit.
4.If add an air compressor, and connect with hammer bit, the HRMC-1200 can do down-the-hole hammer drilling.
5.The power of the rig comes from the independent deck Diesel engine.
6.The rig is mainly used for water well, construction, national defense building foundation, geothermic well and other foundation working;
7.After more than 30 years of market inspection, this rig with reliable quality, simple operation, low maintenance costs. Favored by international well drilling companies in Africa, Russia and Central Asia.
Product Parameters
Technical parameter |
Max drilling depth (M) |
1200 |
Borehole diameter range (mm) |
190-800 |
Single rope lifting capacity of main winch(T) |
8 |
The capacity of main winch(T) |
48 |
Single rope lifting capacity of vice winch(T) |
5 |
The capacity of vice winch(T) |
25 |
The lifting capacity of hook(T) |
60 |
The bearing capacity of mast (T) |
60 |
The height of mast (M) |
10-15 |
Drilling pipe (mm) |
Ф89/Ф114/Ф127 |
Mud pump |
Max flow rate (L / min) |
1500 |
Max discharge pressure (Mpa) |
10 |
Truck chassis |
Standard |
Heavy duty commercial 6*4 truck |
Other Options |
Semi trailer or customer own support vehicle/structure |
Drilling power |
the deck engine |
240Kw |
Weight (kg) |
26340 |
Transport size(L*W*H)(mm) |
15500*2500*3900 |
Main products
Our Advantages
WHY CHOOSE HUAUNO MACHINERY?
1.Our aim is to supply the most suitable borehole drilling machine to users.
You can get a full range of product selection advice and product customization without paying any fees.
2.We have 2 groups of design teams. One team of after-sales engineers with more than 30 years of construction experience at home and abroad, other team of designers who graduated from well-known universities and have rich work experience. We will combine a wealth of practical construction experience and the most advanced professional theoretical knowledge to meet your various demands.
3.We are not only familiar with borehole drilling rig, but also familiar with the human environment, construction environment and strata in the construction field at home and abroad. Provide you with the greatest technical support, save costs and create the greatest value with you. Yes, choosing us is your best decision.
4. Support overseas train and maintain. We do ten days overseas train for free,after you buy our machine.
5. One year Warranty. HUANUO knows the various needs of the water well service companies and operators worldwide.
Customers who buy rigs from us can benefit from great saving thus boost their bottom line.
After Sales Service
Complete operation video, online maintenance, on-site maintenance;
Support overseas train and maintain.
FAQ
FREQUENTLY ASKED QUESTIONS
Q: Are you trading company or manufacturer?
A:our factory more than 30 years experience for produce borehole drilling machine.
Q: Are your products qualified?
A:Yes, our products all have gained ISO certificate,and we have specialized quality inspection department for checking every machine before leaving our factory.
Q: How to get a accurate quotation from us ?
A:Please provide us the details for your well or demands for the rigs. such as max drill depth, borehole diameter range.
Q:What’s the shipping cost from china to your country ?
A:We can send machine to your port or door address by sea or truck. please kindly tell us your nearest destination port or address with postcode. we have reliable shipping agent to insure the safe convenient and time delivery.
Q:Do you accept L/C payment ?
A:Yes, normally our payment is 30%+70% T/T ,LC payment is also acceptable
Q:How to operate this machine ?
A:You will get operation video from us, or on-site training
Q:What about commissioning service ?
A: We can offer commissioning service , the buyer need to afford plane tickets.
Q:Do you offer teaching & training ?
A:Yes, Complete operation video, online maintenance, on-site maintenance also support. For more details pls contact with our saler.
Our Service
OUR SERVICES INCLUDED BUT ARE NOT LIMITED TO THE FOLLOWING
1. Purchase Guidance;
We have a group of sales teams with more than 20 years of experience, and they all have experience in drilling wells at at home and abroad. If you don’t know what type of drilling equipment to choose, we can provide a full range of product selection advice. We customize it for you, you can get the most applicable borehole drill rig from us.
2. Training Service
Our technician is available to your site and offer training of how to use our machines.
As well, you may send your technician to our company to learn how to operate machines.
3.Quality Guarantee
We sign the agreement with detailed technical data. Our warranty is 12 months.
An Overview of Worm Shafts and Gears
This article provides an overview of worm shafts and gears, including the type of toothing and deflection they experience. Other topics covered include the use of aluminum versus bronze worm shafts, calculating worm shaft deflection and lubrication. A thorough understanding of these issues will help you to design better gearboxes and other worm gear mechanisms. For further information, please visit the related websites. We also hope that you will find this article informative.
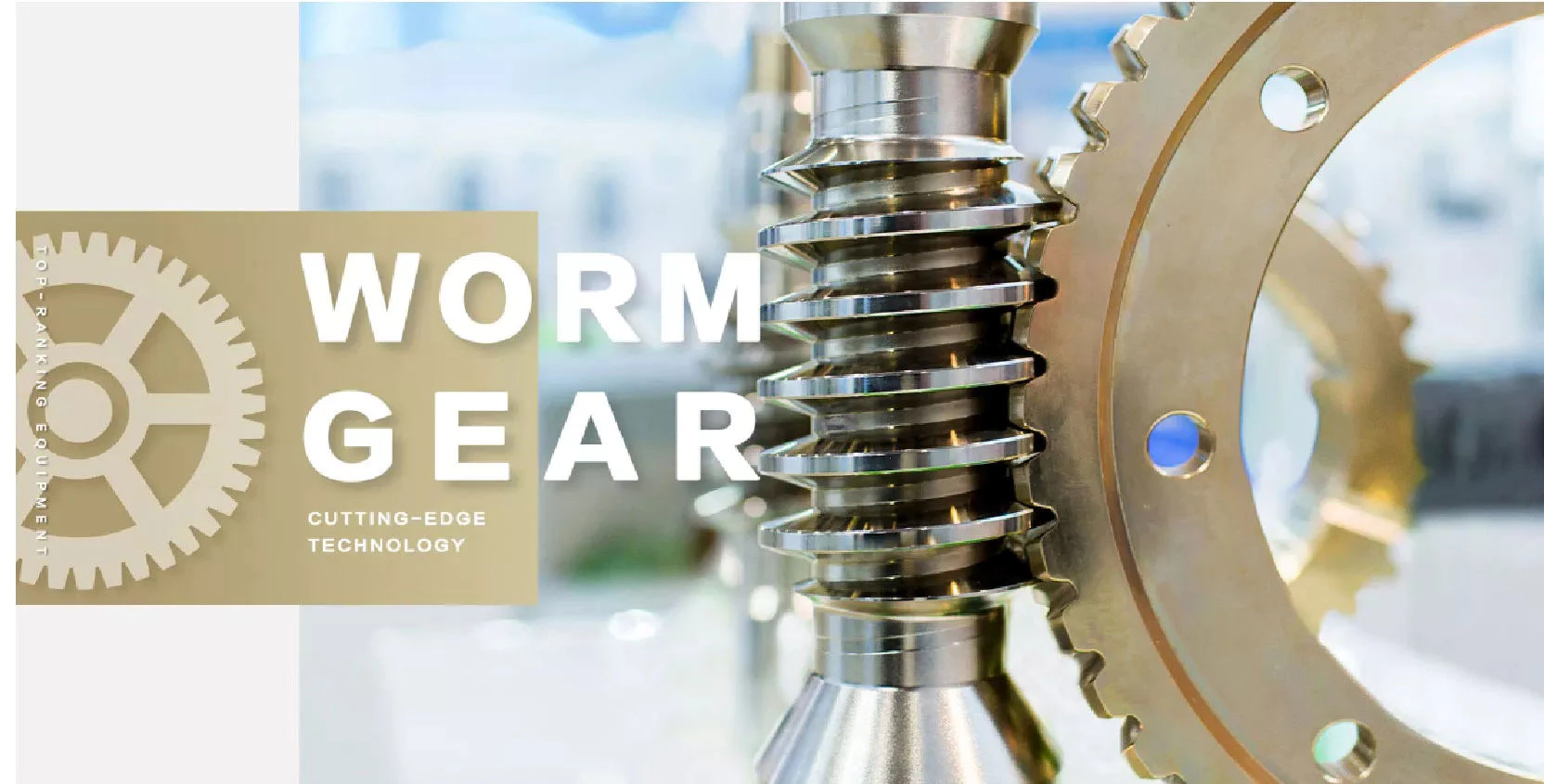
Double throat worm gears
The pitch diameter of a worm and the pitch of its worm wheel must be equal. The 2 types of worm gears have the same pitch diameter, but the difference lies in their axial and circular pitches. The pitch diameter is the distance between the worm’s teeth along its axis and the pitch diameter of the larger gear. Worms are made with left-handed or right-handed threads. The lead of the worm is the distance a point on the thread travels during 1 revolution of the worm gear. The backlash measurement should be made in a few different places on the gear wheel, as a large amount of backlash implies tooth spacing.
A double-throat worm gear is designed for high-load applications. It provides the tightest connection between worm and gear. It is crucial to mount a worm gear assembly correctly. The keyway design requires several points of contact, which block shaft rotation and help transfer torque to the gear. After determining the location of the keyway, a hole is drilled into the hub, which is then screwed into the gear.
The dual-threaded design of worm gears allows them to withstand heavy loads without slipping or tearing out of the worm. A double-throat worm gear provides the tightest connection between worm and gear, and is therefore ideal for hoisting applications. The self-locking nature of the worm gear is another advantage. If the worm gears are designed well, they are excellent for reducing speeds, as they are self-locking.
When choosing a worm, the number of threads that a worm has is critical. Thread starts determine the reduction ratio of a pair, so the higher the threads, the greater the ratio. The same is true for the worm helix angles, which can be one, two, or 3 threads long. This varies between a single thread and a double-throat worm gear, and it is crucial to consider the helix angle when selecting a worm.
Double-throat worm gears differ in their profile from the actual gear. Double-throat worm gears are especially useful in applications where noise is an issue. In addition to their low noise, worm gears can absorb shock loads. A double-throat worm gear is also a popular choice for many different types of applications. These gears are also commonly used for hoisting equipment. Its tooth profile is different from that of the actual gear.
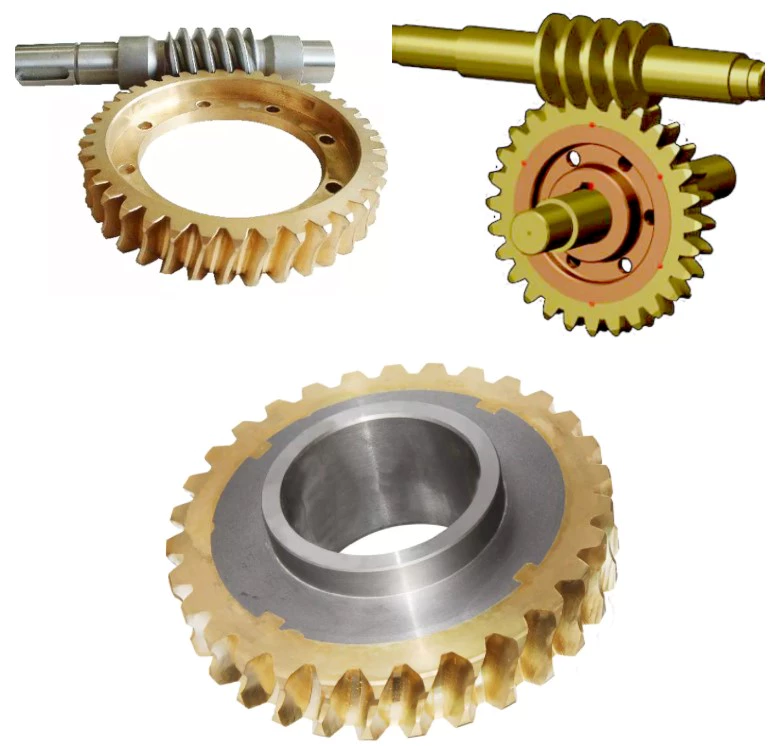
Bronze or aluminum worm shafts
When selecting a worm, a few things should be kept in mind. The material of the shaft should be either bronze or aluminum. The worm itself is the primary component, but there are also addendum gears that are available. The total number of teeth on both the worm and the addendum gear should be greater than 40. The axial pitch of the worm needs to match the circular pitch of the larger gear.
The most common material used for worm gears is bronze because of its desirable mechanical properties. Bronze is a broad term referring to various copper alloys, including copper-nickel and copper-aluminum. Bronze is most commonly created by alloying copper with tin and aluminum. In some cases, this combination creates brass, which is a similar metal to bronze. The latter is less expensive and suitable for light loads.
There are many benefits to bronze worm gears. They are strong and durable, and they offer excellent wear-resistance. In contrast to steel worms, bronze worm gears are quieter than their counterparts. They also require no lubrication and are corrosion-resistant. Bronze worms are popular with small, light-weight machines, as they are easy to maintain. You can read more about worm gears in CZPT’s CZPT.
Although bronze or aluminum worm shafts are the most common, both materials are equally suitable for a variety of applications. A bronze shaft is often called bronze but may actually be brass. Historically, worm gears were made of SAE 65 gear bronze. However, newer materials have been introduced. SAE 65 gear bronze (UNS C90700) remains the preferred material. For high-volume applications, the material savings can be considerable.
Both types of worms are essentially the same in size and shape, but the lead on the left and right tooth surfaces can vary. This allows for precise adjustment of the backlash on a worm without changing the center distance between the worm gear. The different sizes of worms also make them easier to manufacture and maintain. But if you want an especially small worm for an industrial application, you should consider bronze or aluminum.
Calculation of worm shaft deflection
The centre-line distance of a worm gear and the number of worm teeth play a crucial role in the deflection of the rotor. These parameters should be entered into the tool in the same units as the main calculation. The selected variant is then transferred to the main calculation. The deflection of the worm gear can be calculated from the angle at which the worm teeth shrink. The following calculation is helpful for designing a worm gear.
Worm gears are widely used in industrial applications due to their high transmittable torques and large gear ratios. Their hard/soft material combination makes them ideally suited for a wide range of applications. The worm shaft is typically made of case-hardened steel, and the worm wheel is fabricated from a copper-tin-bronze alloy. In most cases, the wheel is the area of contact with the gear. Worm gears also have a low deflection, as high shaft deflection can affect the transmission accuracy and increase wear.
Another method for determining worm shaft deflection is to use the tooth-dependent bending stiffness of a worm gear’s toothing. By calculating the stiffness of the individual sections of a worm shaft, the stiffness of the entire worm can be determined. The approximate tooth area is shown in figure 5.
Another way to calculate worm shaft deflection is by using the FEM method. The simulation tool uses an analytical model of the worm gear shaft to determine the deflection of the worm. It is based on a two-dimensional model, which is more suitable for simulation. Then, you need to input the worm gear’s pitch angle and the toothing to calculate the maximum deflection.
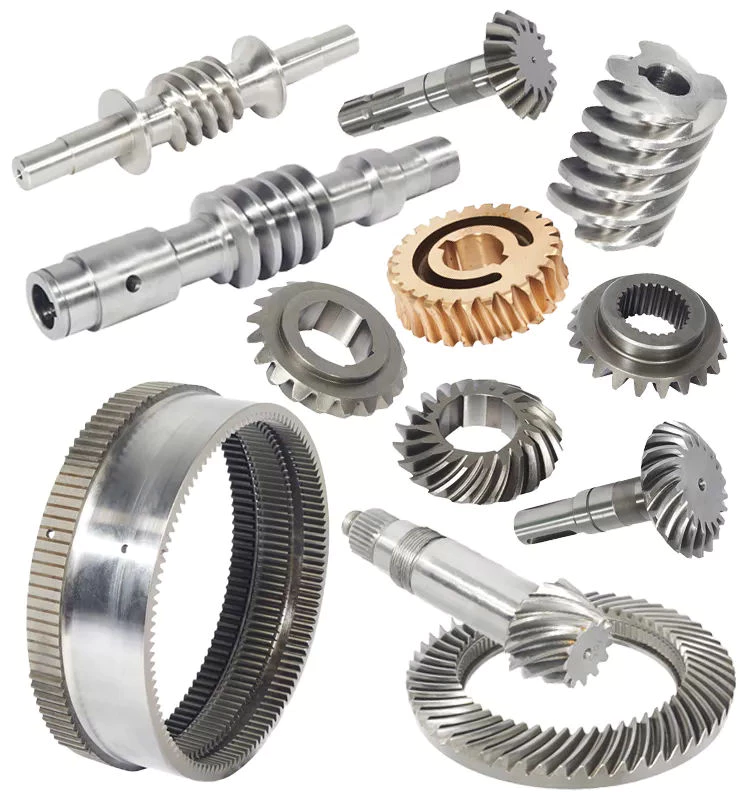
Lubrication of worm shafts
In order to protect the gears, worm drives require lubricants that offer excellent anti-wear protection, high oxidation resistance, and low friction. While mineral oil lubricants are widely used, synthetic base oils have better performance characteristics and lower operating temperatures. The Arrhenius Rate Rule states that chemical reactions double every 10 degrees C. Synthetic lubricants are the best choice for these applications.
Synthetics and compounded mineral oils are the most popular lubricants for worm gears. These oils are formulated with mineral basestock and 4 to 6 percent synthetic fatty acid. Surface-active additives give compounded gear oils outstanding lubricity and prevent sliding wear. These oils are suited for high-speed applications, including worm gears. However, synthetic oil has the disadvantage of being incompatible with polycarbonate and some paints.
Synthetic lubricants are expensive, but they can increase worm gear efficiency and operating life. Synthetic lubricants typically fall into 2 categories: PAO synthetic oils and EP synthetic oils. The latter has a higher viscosity index and can be used at a range of temperatures. Synthetic lubricants often contain anti-wear additives and EP (anti-wear).
Worm gears are frequently mounted over or under the gearbox. The proper lubrication is essential to ensure the correct mounting and operation. Oftentimes, inadequate lubrication can cause the unit to fail sooner than expected. Because of this, a technician may not make a connection between the lack of lube and the failure of the unit. It is important to follow the manufacturer’s recommendations and use high-quality lubricant for your gearbox.
Worm drives reduce backlash by minimizing the play between gear teeth. Backlash can cause damage if unbalanced forces are introduced. Worm drives are lightweight and durable because they have minimal moving parts. In addition, worm drives are low-noise and vibration. In addition, their sliding motion scrapes away excess lubricant. The constant sliding action generates a high amount of heat, which is why superior lubrication is critical.
Oils with a high film strength and excellent adhesion are ideal for lubrication of worm gears. Some of these oils contain sulfur, which can etch a bronze gear. In order to avoid this, it is imperative to use a lubricant that has high film strength and prevents asperities from welding. The ideal lubricant for worm gears is 1 that provides excellent film strength and does not contain sulfur.

